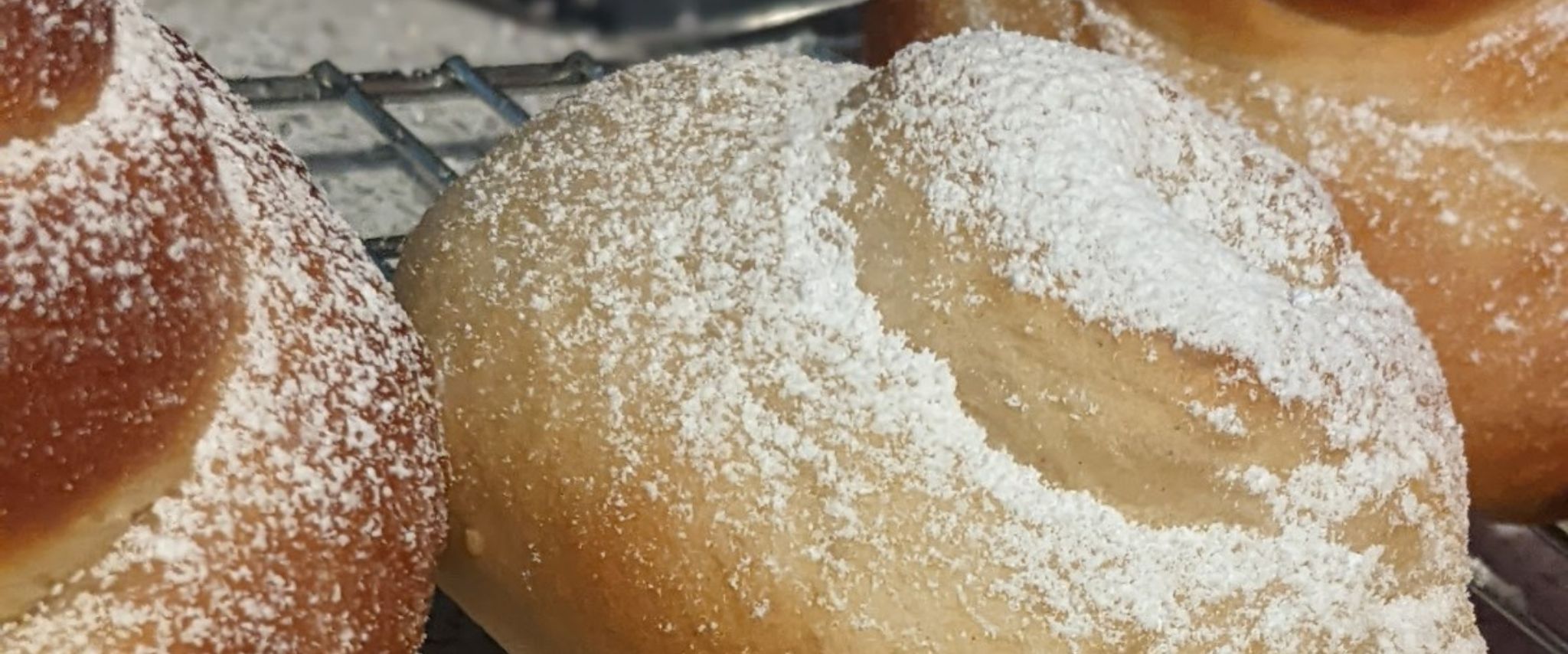
Environmental Monitoring
Monitoring temperatures, humidity, and air quality can enhance the quality of food production and guarantee that proper storage and cooking conditions are being met. Additionally, tracking sound levels can contribute to maintaining a safe and healthy workplace environment.
To prevent wastage of produce, it is important to monitor the storage of ingredients and final products. External temperature probes can be used to monitor refrigerators and storage cupboards. You can set up automated alerts to email or text staff when the correct temperatures are not being maintained. By detecting these issues early, you can ensure that products and ingredients are stored at their best, reducing the number of losses due to incorrect temperatures. Humidity can also affect buildings, people, and products. High humidity can cause dampness and even mould, while low humidity can cause dry air and make people feel unwell. Maintaining humidity levels, especially in food production, can improve productivity and the quality of produce.
In food production, certainly, when powder or flower is used, requires proper ventilation to maintain a clean air supply. Working within a production factory with a lot of airborne powder or flower can cause staff to have difficulty breathing, start coughing, and may cause eye irritation. Lowering the chance of this happening through the right level of ventilation will make the environment safer and improve productivity.
By monitoring sound levels, you can ensure that health and safety requirements are met and that staff have the appropriate PPE when necessary.
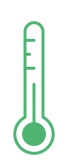
Temperature
ENV01 incorporates onboard temperature and humidity as well as an external probe allowing you to measure the temperature of what you require such as; room temperature, temperature of machinery, or the temperature of certain components.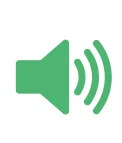
Sound
If your company has a noisy environment due to heavy machinery use this parameter to record exactly how loud it gets and alert you if thresholds are exceeded. This can be used to maintain sound regulations in the workplace.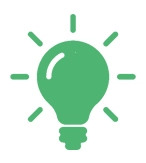
Light
Monitoring light levels through the onboard sensor provides an assessment of the installed location.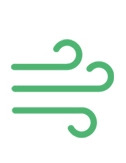
Air Quality
Air Quality is important especially when working in production and manufacturing. Continuous monitoring of airborne particles provides health and safety benefits. This sensor can measure PM2.5 and PM10 particulates.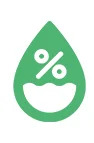
Humidity
Humidity can effect many things including corrosion and contamination. Keeping an eye on how humid your workspace is can help.Order your OpenSmartMonitor sensor via the Devtank website.
Energy and Machine Monitoring
To better manage your energy costs, it’s important to keep track of your electricity, water, and gas usage. By doing so, you can identify areas where you may be wasting energy – such as leaving lights or heating on overnight – and also spot potential leaks in your water or gas supply. By catching leaks early, you can save a significant amount of money on your bills, as these issues can go unnoticed for months and cost you hundreds or even thousands.
Monitoring your machines across production lines can lead to improved efficiency, lower energy costs, and enable predictive maintenance. By tracking the energy usage of your machinery, you can identify any inefficiencies that may be causing high costs. Monitoring various parameters across your machinery can help you identify early signs of faults and necessary repairs, allowing you to schedule maintenance before unexpected breakdowns occur. Automating alerts can make this process even more reliable, potentially spotting issues earlier than a human could. By using a browser-based dashboard, you can remotely monitor all the data collected by your sensors, making it easy to keep an eye on your business from anywhere at any time.
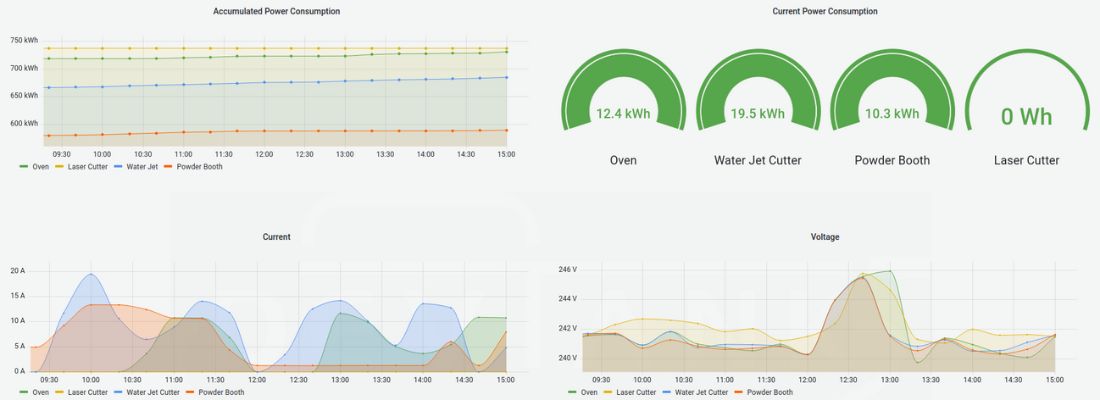
Predictive Maintenance
By utilizing machine monitoring alongside automated alerts, you open your business to predictive maintenance. Predictive maintenance within food production will give you more detailed insights into when your machinery will need repairs or some general TLC. This will help you build a better maintenance schedule and lower your chances of unexpected breakdowns.
Contact our team for more information and discuss how it could benefit your business